Creating a Bone Anchor for At-Risk Patients
For my senior engineering capstone design project at Thayer, I teamed up with four colleagues to design a novel bone anchoring system for osteopenic patients undergoing rotator-cuff repair.
The Context.
Date: fall ‘17 - spring ‘18
Location: Dartmouth College, NH
A two-term senior project developing a product for a client in industry
My Role.
Product design
Rapid prototyping & testing
Automated manufacturing process development & machining
Secondary research
User research
Market analysis
Presentation
The Problem
In the United States, one in five adults over 50 experience full-thickness tears in their rotator cuff, the set of muscles and tendons controlling the human shoulder. These injuries cause significant discomfort and disability, and typically require corrective surgery which costs $5,000-16,000.
In surgical rotator cuff repair, sutures threaded through the tendon are anchored onto the humeral head to promote regrowth of the bone-tendon connection. Reduced bone density, however, lowers bone strength and increases the risk of anchor failure by “pullout” from the humerus, and among those over 50, more than half have decreased bone mass.
The Solution: Concepts & Prototypes
We asked: how might we develop a safe, cost-effective bone anchor that reduces pull-out in high risk patients?
We came up with all sorts of crazy ideas: corkscrews, different shaped anchors, injectable anchors, and even an origami-inspired disk that would expand beneath the bone surface.
To test our ideas, we analyzed failure modes, conducted secondary research, and made a Pugh Matrix of early alternatives. We then developed models of our top ideas in Matlab and Solidworks to test early prototypes against our design criteria, before ultimately pursuing a design where surgeons can inject bone cement through the anchor into the bone.
Fabrication & Testing
Fabrication
While half of the team focused on developing a better model for osteopenic bone by testing various acid treatments on animal bone, two members and I focused on anchor manufacturing, rapid prototyping, and mechanical testing of our anchors.
We manufactured high-quality anchors on a lathe (Figure A (a)) and rapidly prototyped anchors using a CNC Mill (Figure A (b)) and a modified version of our Solidworks model (Figure B).
User Feeback
We involved surgeons throughout the process to ensure we were meeting their and their patient’s needs. This involved several surveys, interviews, and follow-ups.
One of the highlights of the project was getting the opportunity to watch a live rotator-cuff repair surgery and seeing the bone anchor insertion process in realtime!
Injection Testing
I experimented with various bone cements and a thermoplastic to identify viable materials for use. The material had to meet several design criteria, including:
Viscosity & inject-ability: I performed flow sweep tests on a rheometer to characterize the viscosity and working time of materials. I also tested the usability of each material by injecting it directly into bone models and through our prototypes with a syringe. Any materials that were too viscous or difficult to work with were excluded as candidates.
Strength characteristics: I machined a mold to create larger, hardened bone cement samples upon which I performed 4-point bend tests of hardened injectables to understand their physical attributes.
Necrosis testing: bone cement hardens in an exothermic polymerization reaction and thermoplastics must be melted before being injected into bone. This presents a risk of destroying the bone if temperatures exceed a certain threshold. I recorded the temperatures of polymerization and melting temperature of the bone cements and thermoplastic, respectively, to ensure they were safe to use.
In the end, polymethyl methacrylate (PMMA), a common bone cement, met our design and safety requirements and was used in our final design.
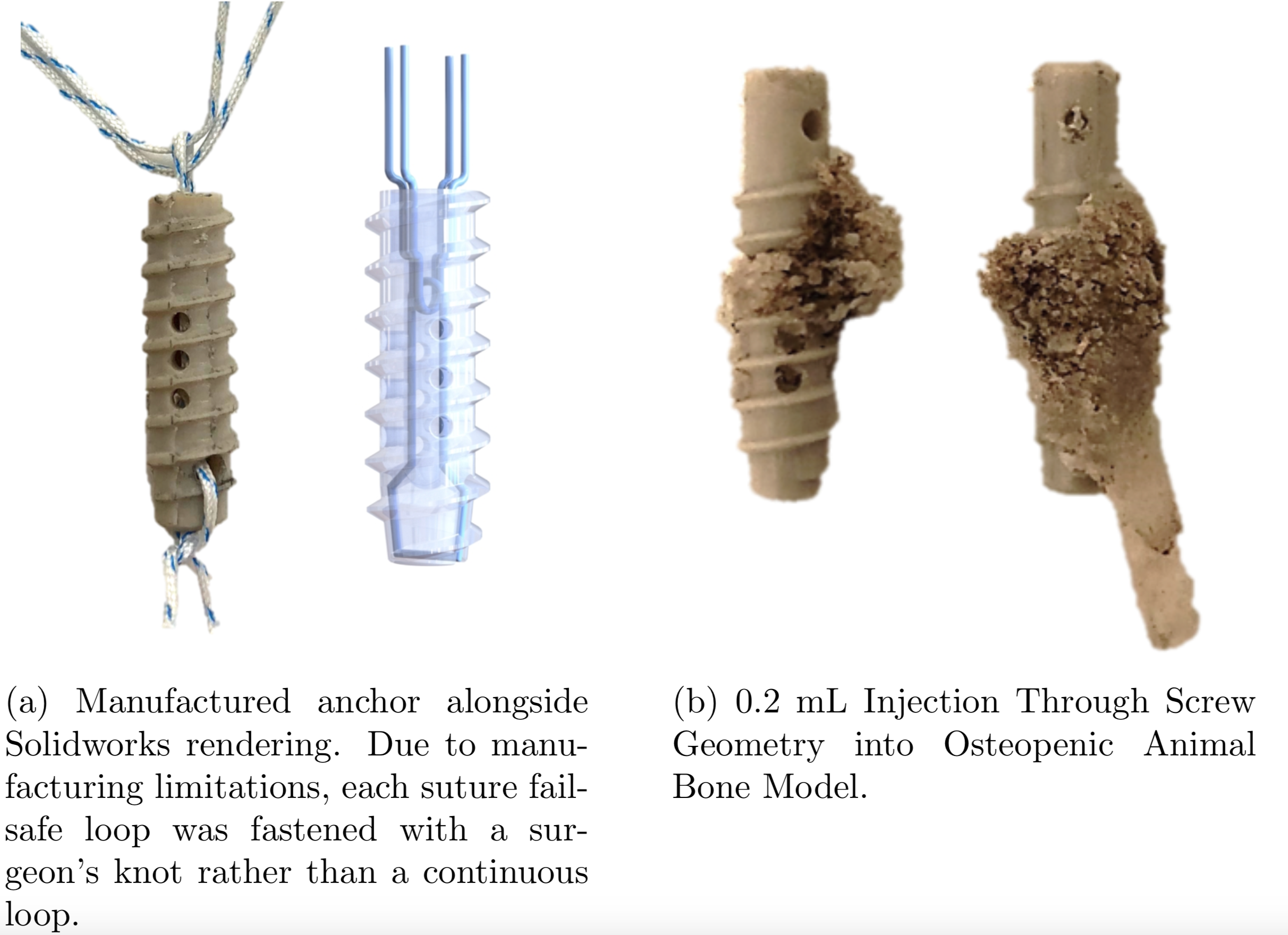
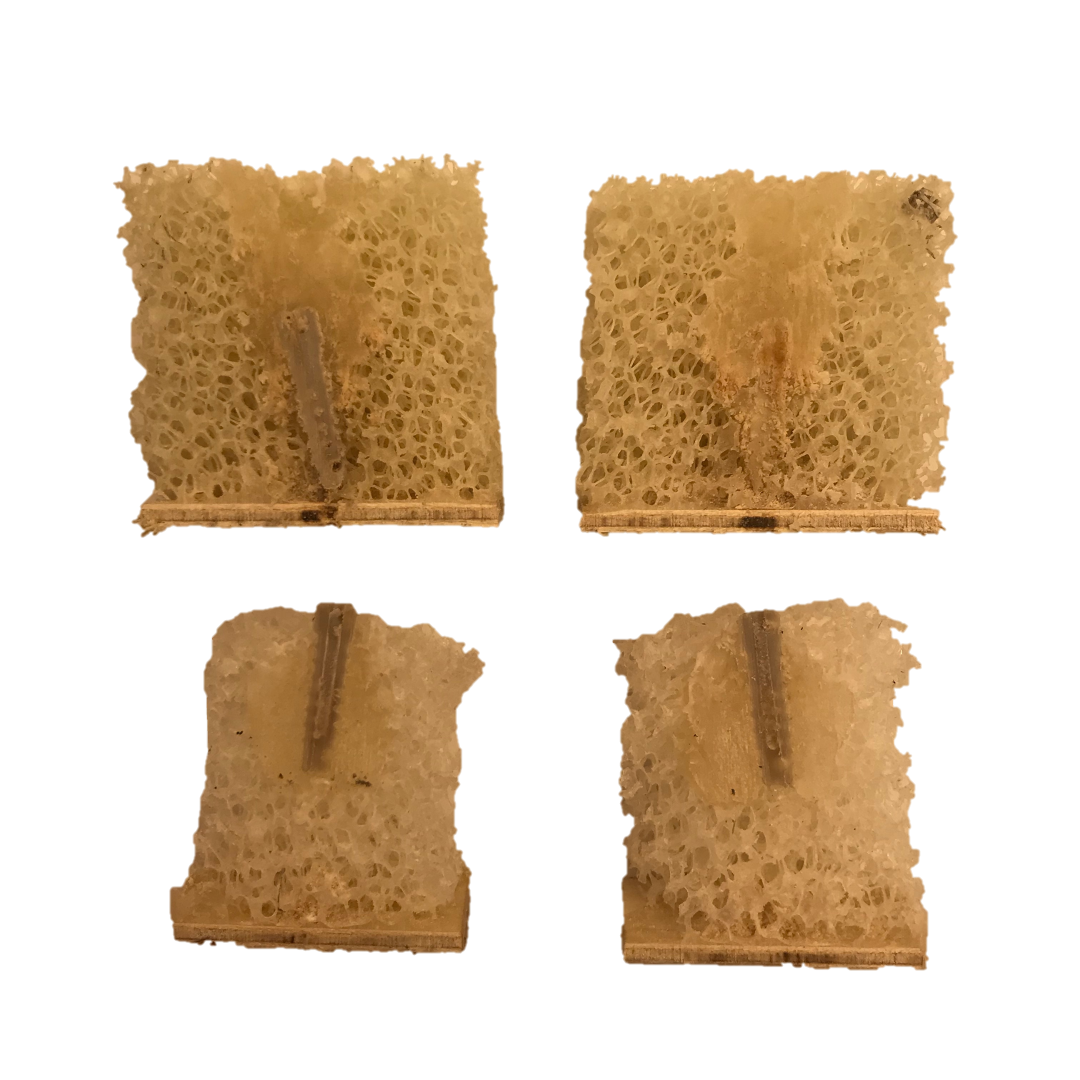
Injection through anchor into bone model
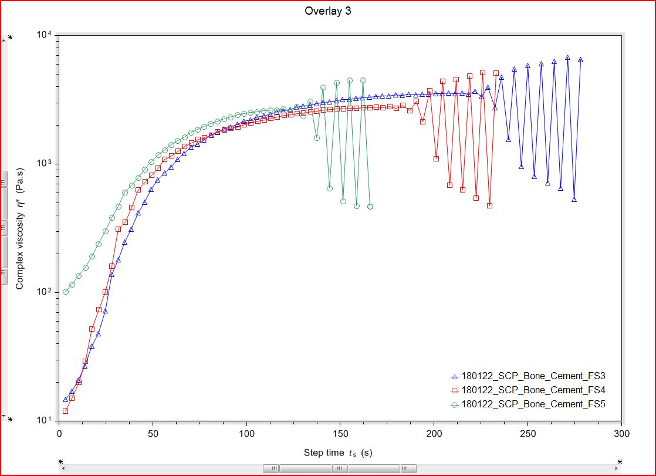
PMMA Viscosity Testing; viscosity increased as samples hardened over time
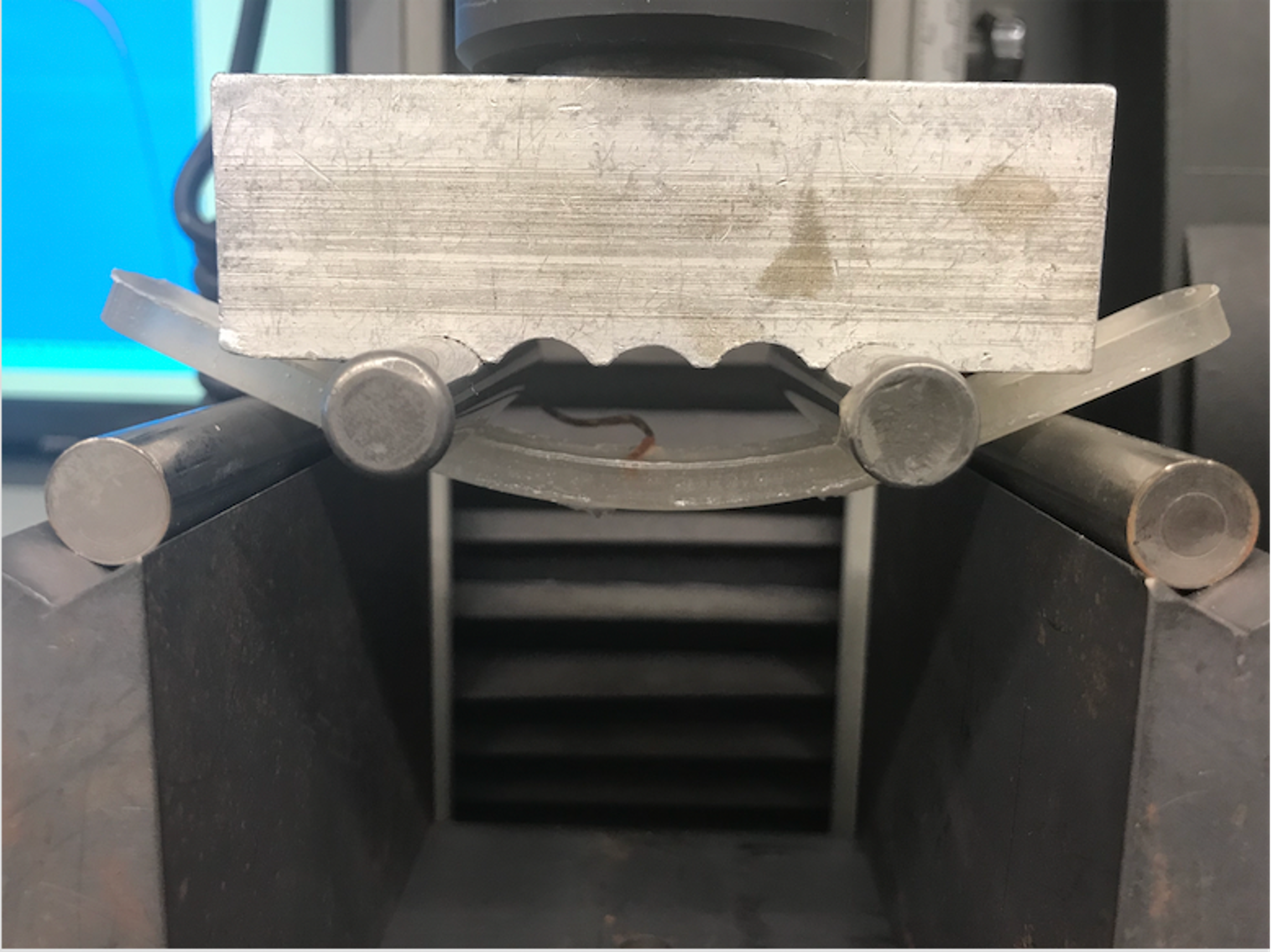
4 point bend test
Strength Testing.
To ensure our anchor was secure and wouldn’t pull out of the patient’s bone, we set up a rig with our anchors imbedded in synthetic bone model on an Instron and tested their pullout strength.
We tested several bone anchors and cements in various bone models against state-of-the-art bone anchors and used the results to iteratively improve our prototypes.
The Home Strech
Our final anchor design featured a hollow center and pores through which PMMA could be injected but did not interfere with standard anchor functioning. This allowed surgeons the option to use the anchor with or without injection depending on patient need.
Image: Pull-out strength in high (10 PCF) and low (5 PCF) density bone model
Our anchor demonstrated pullout performance equal to or exceeding state of the art anchors without injection, and 5-times stronger when augmented with bone cement injection.
As a final touch, we developed an insertion mechanism in Solidworks, featuring a cannula to inject cement through and a hex drive to insert the anchor.
If you’d like to learn more, you can read our full 65-page final report on the project here.
Why it matters.
I believe designing products and services with the end-user in mind is essential to the design process, making sure to include groups of people that may be overlooked or underserved. Oftentimes, the elderly fall into this category. Bone anchor pullout is painful and debilitating, but avoidable.
On a personal note, this project was special to me because it was my most extensive undergraduate design project. It was an exciting chance to gain experience in the design process all the way from ideation to a final product.